
WIRE WRAP SCREEN
Our wire-wrap screens are a versatile, cost effective and viable sand control option in a variety of well environments. What you will receive is a balance between effective sand control and long term well productivity at an affordable budget.
Wire-wrap screens can be fully customized to meet any specific well application. They feature strong assemblies, are resistant to erosion, and cannot be plugged by fines or produced solids.
An exclusive slip-ring design isolates the wire-wrap jacket from mechanical loads applied to the screen assembly (i.e. compression, tension, or torque), maintaining efficient sand control.
The typical screen unit arrangements are 32 ft of jacket on 38 ft of base pipe and 16 ft of jacket on 20 ft of base pipe, but any length of handling area for torque tongues can be ordered. The protective shroud can be perforated or louvered and is designed to accommodate running cables.
Main Applications
-
Stand Alone Screens
-
Open and Cased hole Gravel Packs
-
Cased Hole Frac packs
Strengths
-
Longeve in harsh production environment
-
Easy handling and fast installation
-
Reliability and cost effective

Characteristics
-
Multiple options for wire width and height in jacket and rib construction
-
They include the slip rings, fin-type or spiral centralizers
-
Direct Wrap option for increased robustness
-
Perforated or louvered shroud option for extra protection with or without fiber-optic cable
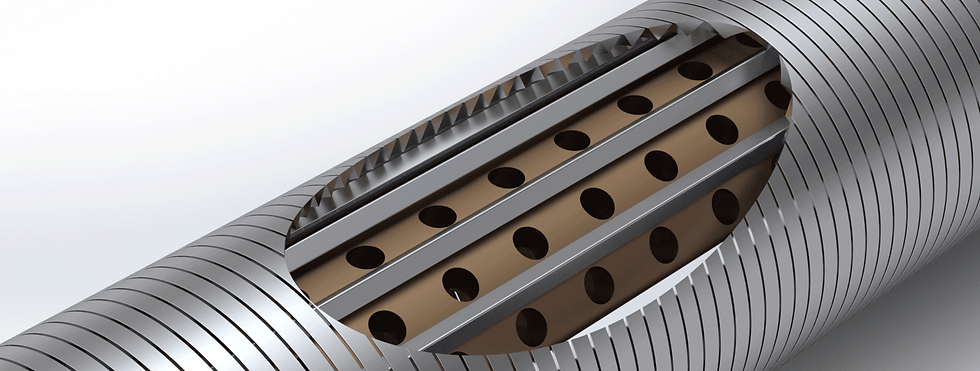


Manufacturing & Quality
CP utilizes the latest technology in optical measurement to achieve assurance on slot tolerance. The optical measurement system has a resolution of 5µm providing a superior inspection methodology rather than feeler gauge or optical lube much used by other manufacturers.
The profile wires are the key to ensure slot accuracy, with a 100% continuous laser micrometer measurement: our profile wires are manufactured using stringent processes to ensure metallurgical integrity in grain size, control of hardness and cleanliness, providing high tolerance on the size.
Prevention of SCC (Stress Corrosion Cracking) comes thru annealing process, while the cleanliness of the wire helps ensure consistent weld ability.
Optical slot inspection indeed is done using a calibrated vision measurement system with a resolution of 5μm, so slot measurements can be made to comply with ISO17824, API 19SS Q1, client specific QCP requiring 100% slot measurement in a single plane or greater. A Statistical Process Control is used to define the screen slot and is supplied with the Quality Dossier.
Pre-production checks performed on the wires are:
-
100% measurement of wire head, width & depth via laser micrometer;
-
Testing and verification on wire hardness, PMI (Positive Material Identification), tensile strength, yield strength, elongation and profile cross-section dimensions are all met;
-
Prevention of SCC (Stress Corrosion Cracking) by using Strand (continuous) annealing of wire;
-
Cleanliness of the wire to ensure consistent weld ability;
-
Weld strength test every joint.
THROUGH TUBING SYSTEM
Thru-tubing screens are miniatured version of the screen , designed to run inside existing tubing string as small as 2-3/8”.Screens are installed to perform re-medial sand control inside a failed screen or tubing where sand control was not installed.Thru-tubing screens can be gravel packed or run as stand-alone screens, depending on the sand conditions. Sizes ranges from 1” base pipe OD to 1.9”, with a product OD of 1.5” to 2.4”.